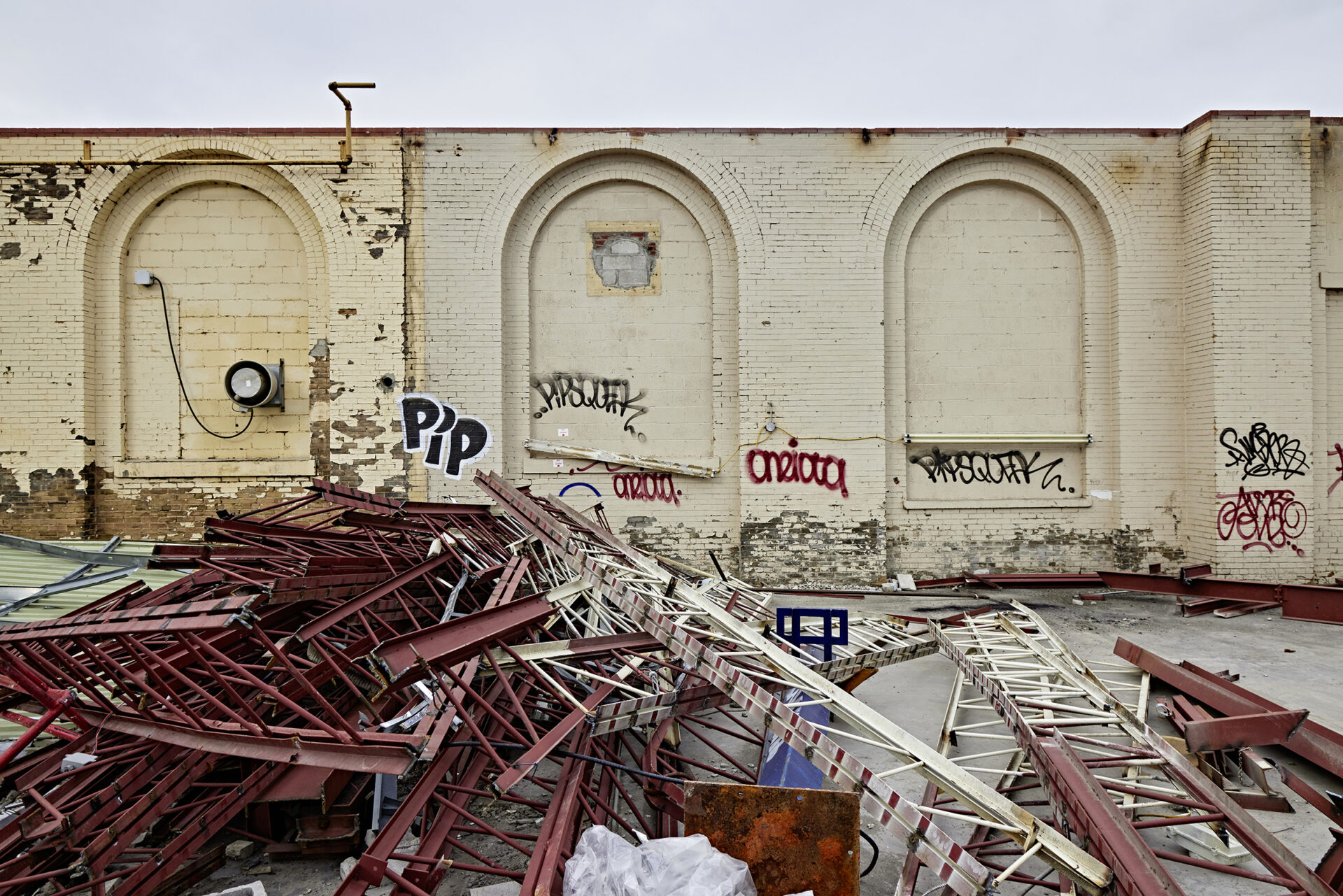
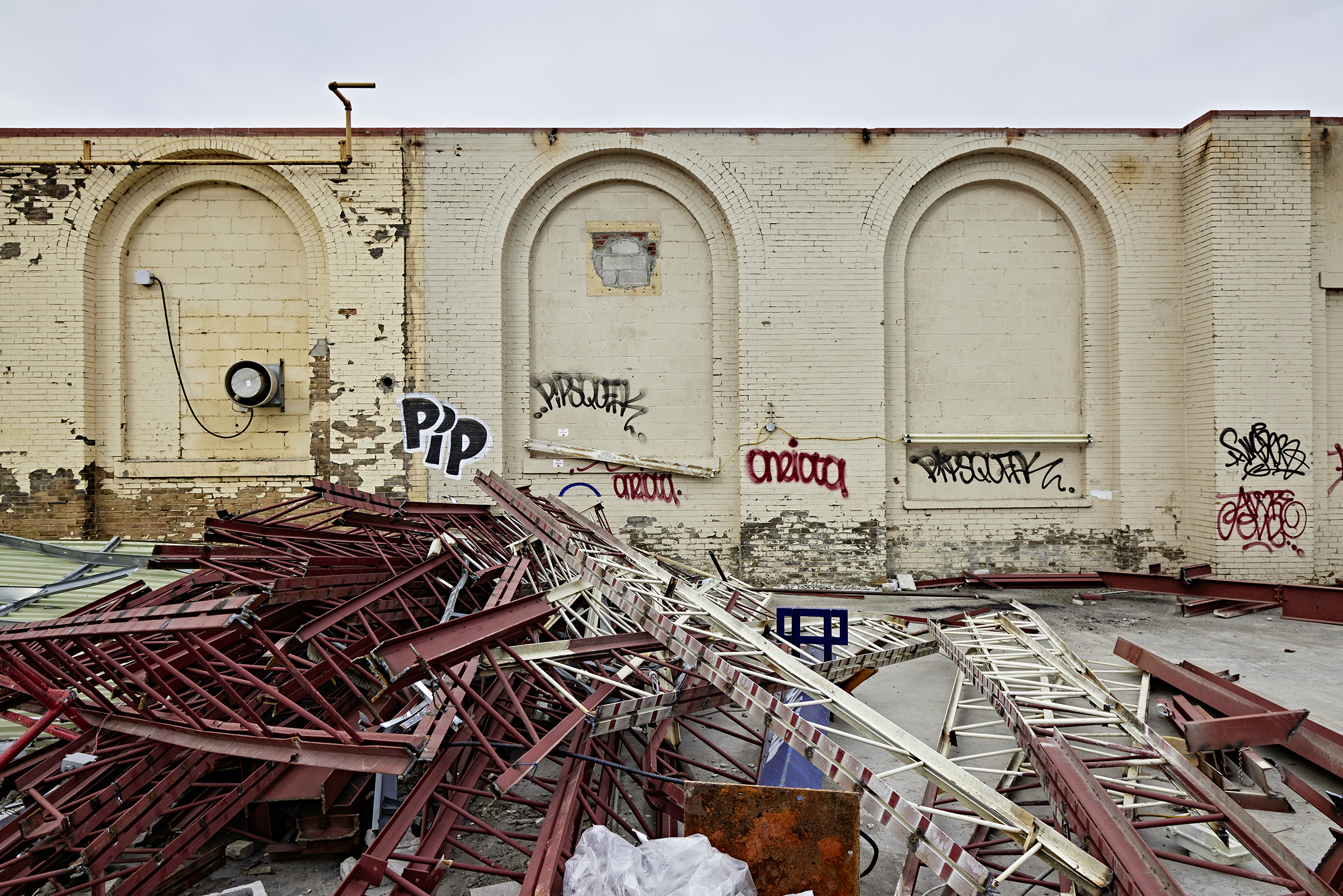
At this year’s DesignTO Festival, attendees had the opportunity to join a tour around the Wellington Destructor, a century-old garbage incinerator in downtown Toronto poised to become a new community hub.
During the tour, large piles of similar materials could be spotted throughout the site – an uncommon scene during demolition.
We wanted to find out why.
Through the last century of Toronto’s growth, construction has followed a traditional path: the buildings and landscape that existed on a given site are demolished, those materials are destroyed and taken away to landfill, and a new building is constructed in its place with brand-new materials made in a factory. The growth of our city stems from acquiring and using new materials to create buildings of social and economic value.
Toronto needs to house 3 million new people by the same year it reaches net-zero, and building more while polluting less is among the greatest challenges of the next generation. The extraction and production of every new building material releases excess carbon into the atmosphere. Excess carbon emissions then trap excess heat in our atmosphere, and the building industry is responsible for 39% of worldwide greenhouse gas emissions. In the pursuit of net-zero emissions, it is imperative that city builders work toward embracing a circular economy: deconstructing, salvaging, sorting and reusing good materials wherever possible.
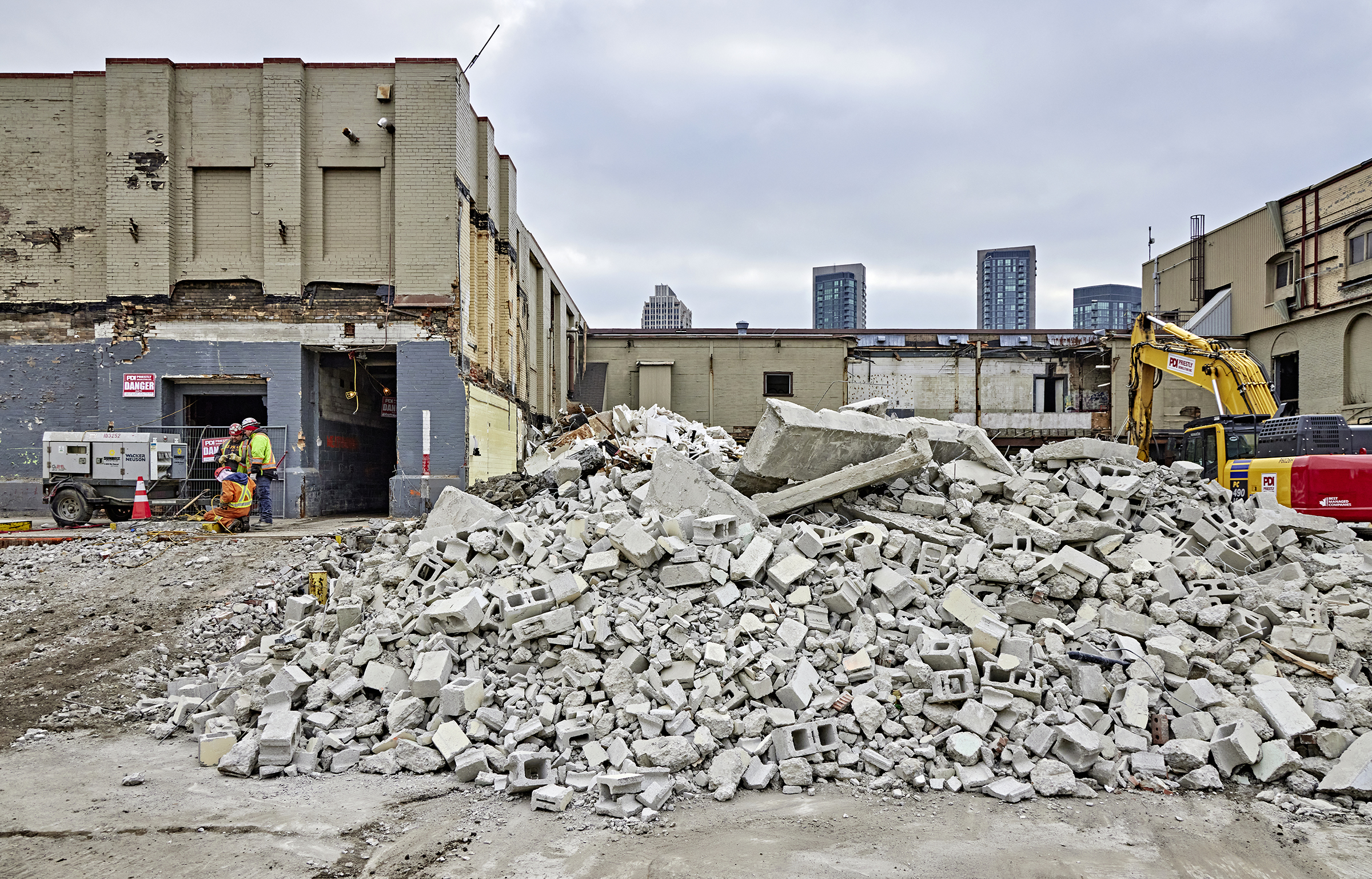
TAS, an unconventional impact company that uses real estate as a tool to drive profit and purpose, is beginning this journey with the master-planned community at 2 Tecumseth, which the historic Wellington Destructor is part of. Other buildings like the abattoir, barns and cold storage facilities that have occupied the site since the late-1800s are full of bricks, wood beams, concrete foundations and fixtures that not only emitted atmospheric carbon when they were first produced but are still valuable and ripe for repurposing over a century later.
Collaborating with the landscape team at Public Work, designers inspected the existing site and earmarked potential materials for reuse in sitework, berm walls, installations and public spaces. Once the initial design proposals were made, TAS used Life-Cycle Assessment software to estimate those materials’ embodied carbon footprints. They then engaged their demolition consultants to gauge the feasibility of cleanly extracting each component and assessed the carbon and cost tradeoffs of the more challenging materials to understand the environmental benefit. With planning and thoughtful design, not only will over 6000 tons of material be directed away from landfill, but hundreds of tons of greenhouse gas emissions are crucially being avoided through the reduction of new materials.
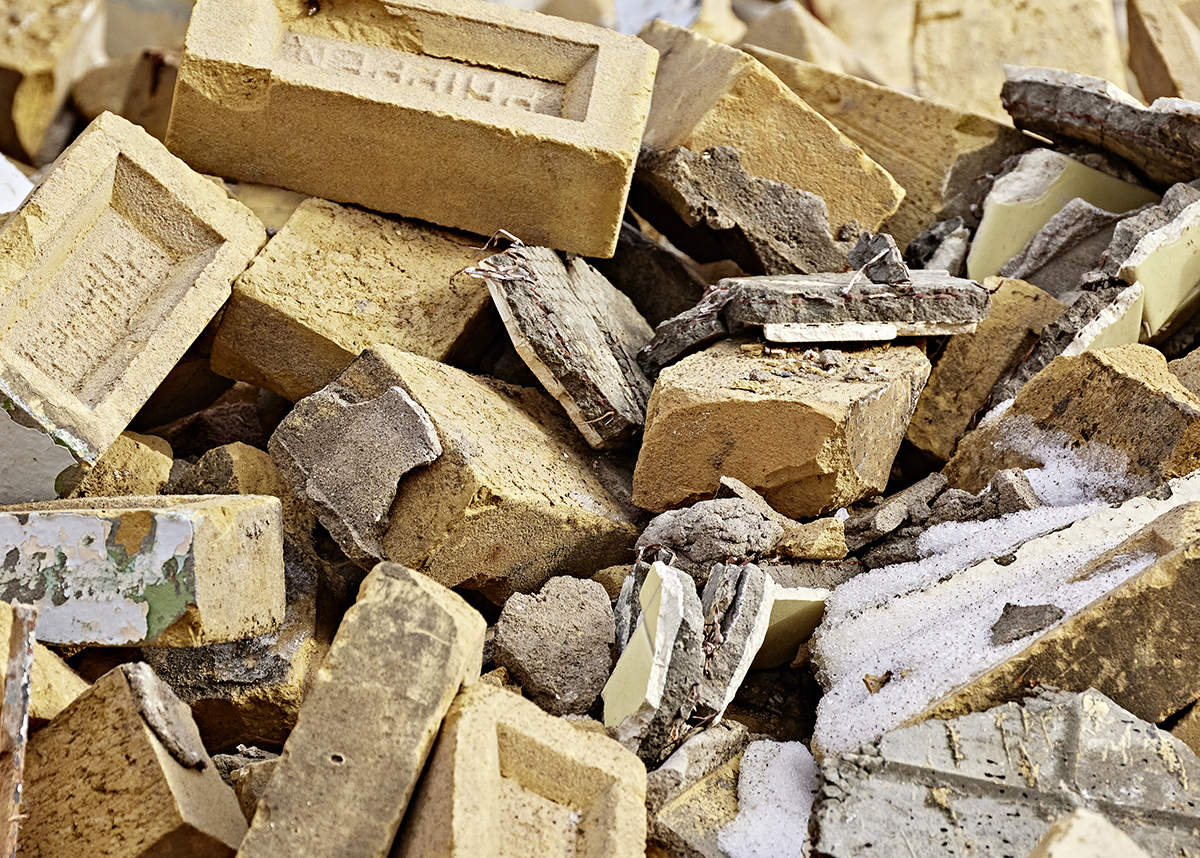
Material reuse requires upfront planning, collaboration across disciplines, and space to store materials. More opportunity can be had in integrating existing buildings, landscape elements and fixtures into new designs if we quantify what we have before we begin schematic design, and work together with engineering, design, demolition and construction consultants towards better solutions. Land is also needed to contain the materials extracted from the old buildings until they’re reused; as a developer working on a large site, TAS is able to store this brick, wood, concrete and metal directly on-site and out of the way of construction crews.
TAS is committed to testing this process and learning from their successes and challenges. Follow along as TAS further innovates the development process towards this necessary and exciting future.
TAS is an unconventional impact company that uses real estate as a tool to drive profit and purpose. A champion of conversation and collaboration, TAS focuses on tackling climate change, broadening affordability and equity, and building social capital to create neighbourhoods – and ultimately cities – where people can thrive and belong.